Installation Instructions
Pre-installation Guidelines
- Complete all necessary hazard mitigation, monitoring and control action.
- Do not install any parts or modify a previous Controller Installation without assessment and advice from Banlaw.
- ResTrack Lite Controller is not intended for use in high-vibration environments, such as mobile vehicle applications.
- Do not install any damaged or faulty parts.
- Do not install electrically incompatible parts to the Banlaw ResTrack Lite Controller.
- Do not install parts that have not been approved by Banlaw.
- Do not install or modify any electrical parts if you are not certified to do so.
- Only engage pipework threads of the same thread type. Ensure all threaded connections are clean and in good condition. Avoid over-tightening. Use suitable thread sealant or tape.
- Ensure to position the ResTrack LiteTM controller out of direct sunlight to increase reliability and prolong hardware life.
- Ensure all fasteners used match the Controller’s mounting points.
- Ensure correct tools and torque are used to tighten all fasteners.
- The enclosure is IP66 rated from factory. Please do not modify the enclosure as this may result in the breach of enclosure integrity and may
- Ensure isolation procedures has been completed prior to affixing all the mechanical and electrical components.
Generic ResTrack Lite System Installation Procedure
- The BRTL Controller cannot be installed in a hazardous zone.
- All power inputs/outputs shall only be connected by a qualified electrician.
- All air elimination and straining devices shall be installed to suppliers’ specification.
- Complete all necessary hazard mitigation, monitoring and control action as per site procedures.
- Unpack the controller and all its associated parts.
- Make a general arrangement of where the controller and all associated components will be mounted.
- Ensure the controller cannot be unintentionally operated or damaged.
- Locate a power source and ensure there is enough provisions to connect the power supply to the BRTLC Controller.
- Ensure that a Y-strainer or a Filter is installed prior to the Flow Meter. Failure to do so may result in flowmeter internals damage.
- Ensure that pipework and components are installed in the following order:
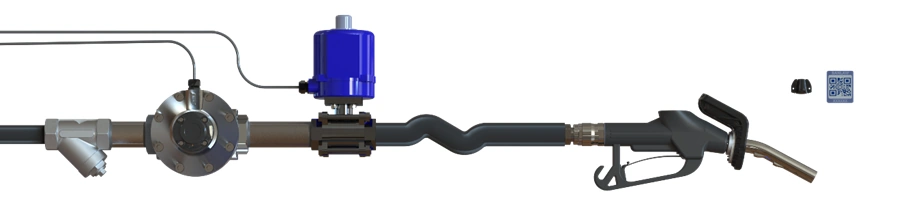
Y Strainer
Flow
Meter
Actuated Valve
Dispensing Nozzle
Generic ResTrack Lite LV Refuelling Arm
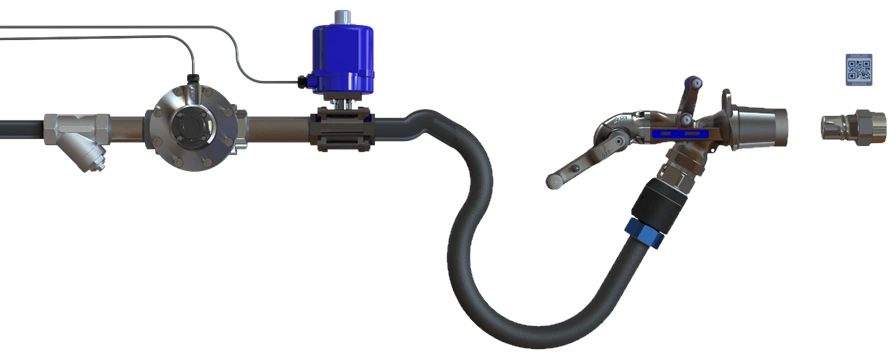
Y Strainer
Flow
Meter
Actuated Valve
Dispensing Nozzle
Generic ResTrack Lite HV Refuelling Arm
BRTLLS01A Level Sensor Installation Procedure
Exploded View and BOM
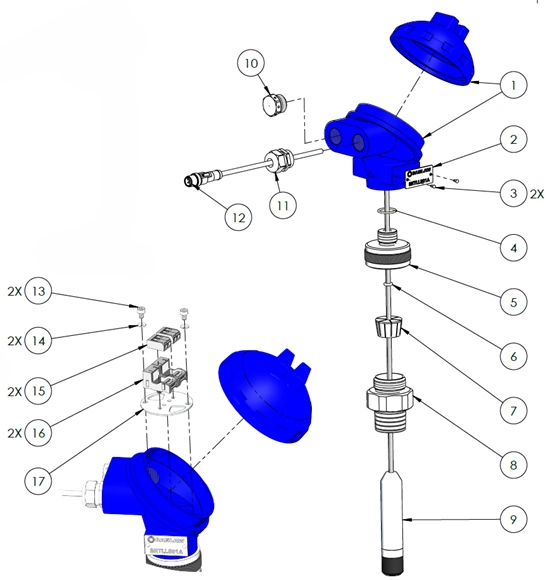
BRTLLS01A Exploded view
ITEM # | DESCRIPTION |
---|---|
1 | PTC HEAD, DUAL PORT |
2 | DATA PLATE, LEVEL PROBE |
3 | SCREW, U-DRIVE, #2 X 3/16" |
4 | ORING BS017 |
5 | ADAPTOR, 5MM GLAND BODY, 1/2" NPS (M) |
6 | ORING BS106V |
7 | COLLET, LEVEL SENSOR, 5MM WIRE |
8 | ADAPTOR, COLLET CLAMP BODY, 1" BSPT (M) |
9 | LEVEL SENSOR |
10 | PLUG, VENTILATION, M20X1.5, 1P67 |
11 | GLAND, COMPRESSION, M20 |
12 | CABLE ASSEMBLY, M12 PLUG, A CODE |
13 | SCREW, SHC, M4X6 LG |
14 | WASHER, SPRING, M4 |
15 | TERMINAL, SPLICE LEVER, 2 POS |
16 | TERMINAL CARRIER, 2 POS |
17 | GLAND PLATE, LEVEL SENSOR |
Package Content
Inside the level sensor pachage, you will find an assembled Level Sensor Head with process connection, and the Level Sensor itself. Follow the installation procedure below to assemble and mount the level sensor on your storage tank.
Level sensor is measuring pressure at the bottom of the storage tank and its output is converted in the % of full. Therefore, shape of the tank is irrelevant and it will be equally efficient in linear (e.g. rectangular) or non-linear (e.g. flat cyllinder) tanks.
Note that maximum tank height is 5m, which is dictated by the length of the provided level sensor.
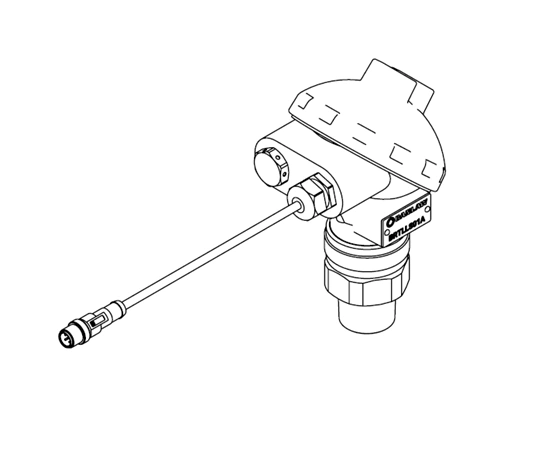
Level Sensor Head
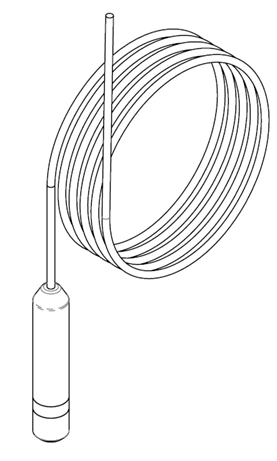
Level Sensor
Level Sensor Installation Procedure
- Disassemble head to retrieve Retaining O-ring “Item 6”.
- Apply thread tape or sealant onto the 1” BSPT(M) thread on “Item 8”.
- Screw “Item 8” into the designated mounting location. (NOTE: Thread Engagement = Turns From Finger Tighten (TFFT) Method: 1.5 – 2.5 turns.)
- Insert the pressure transducer “Item 9” into the tank through “Item 8”.
- Place a mark Point A on the pressure transducer rope when the pressure transducer “Item 9” hits/sits on the bottom of the tank.
- Measure 200mm up from the previous mark Point A and place mark Point C.
- Using job site approved tools to cut the transducer on the Point C.
- Unsheathe 50mm of the cable harness to expose the cables. (NOTE: Ensure not to damage the capillary tube.)
- Unsheathe 10mm of the wires to expose the conductor.
- Measure 100mm down from unsheathed wires and place a mark Point B.
- Slide following items as per sequenced, 200mm into the pressure transducer line:
- the collet, “Item 7”.
- the retaining O-ring, “Item 6”.
- Depress collet, “Item 7” onto Point B. (NOTE: The pressure transducer will now be lying on the bottom of the tank.)
- Slide retaining O-ring, “Item 6” onto collet, “Item 7”
- Screw in “Item 5”, to fully secure the level probe within the tank. (NOTE: Only hand tight is required, when screwing down the “Adaptor, 5mm Gland Body”)
- Remove both M4 x 6 Screw “Item 13” from “Item 1” to allow easier cable entry.
- Feed the cable into the level probe head, “Item 1” and screw it down. (NOTE: Only hand tight is required, when screwing down the “PTC Head”)
- Allow the capillary tube to pass through one of the holes as per indicated in the diagram.
- Terminate the Level Probe onto Position 2 of the terminal splicer “Item 15” as shown in the termination diagram below. (NOTE: Do not terminate white cable from pressure transducer)
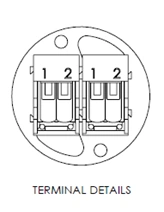
Feed unsheathed
wires through here
Feed capillary
tube through here
- Re-assemble both M4 x 6 Screw “Item 13”.
- Re-assemble “PTC Head” cap.